THE LATEST
NASA Goddard engineer McClelland shifts to AI to design mission hardware
- Written by: Tyler O'Neal, Staff Editor
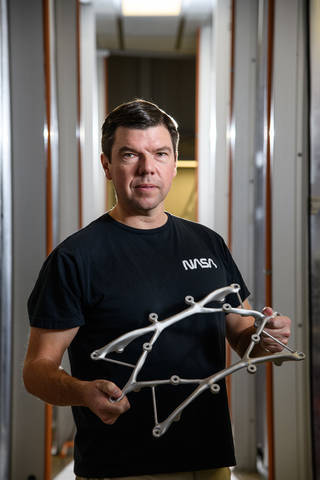
Spacecraft and mission hardware designed by artificial intelligence may resemble bones left by some alien species, but they weigh less, tolerate higher structural loads, and require a fraction of the time parts designed by humans take to develop.
“They look somewhat alien and weird,” research engineer Ryan McClelland said, “but once you see them in function, it makes sense.”
McClelland pioneered the design of specialized, one-off parts using commercially available AI software at NASA’s Goddard Space Flight Center in Greenbelt, Maryland, producing hardware he has dubbed evolved structures.
To create these parts, a computer-assisted design (CAD) specialist starts with the mission’s requirements and draws in the surfaces where the part connects to the instrument or spacecraft – as well as any bolts and fittings for electronics and other hardware. The designer might also need to block out a path so that the algorithm doesn’t block a laser beam or optical sensor. Finally, more complex builds might require spaces for technicians’ hands to maneuver for assembly and alignment.
Once all off-limits areas are defined, the AI connects the dots, McClelland said, producing complex structure designs in as little as an hour or two. “The algorithms do need a human eye,” he said. “Human intuition knows what looks right, but left to itself, the algorithm can sometimes make structures too thin."
These evolved structures save up to two-thirds of the weight compared to traditional components, he said and can be milled by commercial vendors. “You can perform the design, analysis, and fabrication of a prototype part, and have it in hand in as little as one week,” McClelland said. “It can be radically fast compared with how we’re used to working.”
Parts are also analyzed using NASA-standard validation software and processes to identify potential points of failure, McClelland said. “We found it lowers risk. After these stress analyses, we find the parts generated by the algorithm don’t have the stress concentrations that you have with human designs. The stress factors are almost ten times lower than parts produced by an expert human.”
McClelland’s evolved components have been adopted by NASA missions in different stages of design and construction, including astrophysics balloon observatories, Earth-atmosphere scanners, planetary instruments, space weather monitors, space telescopes, and even the Mars Sample Return mission.
Goddard physicist Peter Nagler turned to evolved structures to help develop the EXoplanet Climate Infrared TElescope (EXCITE) mission, a balloon-borne telescope developed to study hot Jupiter-type exoplanets orbiting other stars. Currently, under construction and testing, EXCITE plans to use a near-infrared spectrograph to perform continuous observations of each planet's orbit about its host star.
“We have a couple of areas with very tricky design requirements,” Nagler said. “There were combinations of specific interfaces and exacting load specifications that were proving to be a challenge for our designers.”
McClelland designed a titanium scaffold for the back of the EXCITE telescope, where the IR receiver housed inside an aluminum cryogenic chamber connects to a carbon fiber plate supporting the primary mirror. “These materials have very different thermal expansion properties,” Nagler said. “We had to have an interface between them that won’t stress either material.”
A long-duration NASA Super-Pressure Balloon will loft the EXCITE mission’s SUV-sized payload, with an engineering test flight planned as early as the fall of 2023.
Ideal Design Solution for NASA’s Custom Parts
AI-assisted design is a growing industry, with everything from equipment parts to entire car and motorcycle chassis being developed by computers.
The use case for NASA is particularly strong, McClelland said.
“If you’re a motorcycle or car company,” McClelland said, “there may be only one chassis design that you’re going to produce, and then you’ll manufacture a bunch of them. Here at NASA, we make thousands of bespoke parts every year.”
3D printing with resins and metals will unlock the future of AI-assisted design, he said, enabling larger components such as structural trusses, complex systems that move or unfold, or advanced precision optics. “These techniques could enable NASA and commercial partners to build larger components in orbit that would not otherwise fit in a standard launch vehicle, they could even facilitate construction on the Moon or Mars using materials found in those locations.”
Merging AI, 3D printing or additive manufacturing, and in-situ resource utilization will advance In-space Servicing, Assembly, and Manufacturing (ISAM) capabilities. ISAM is a key priority for U.S. space infrastructure development as defined by the White House Office of Science and Technology Policy’s ISAM National Strategy and ISAM Implementation Plan.
This work is supported by the Center Innovation Fund in NASA's Space Technology Mission Directorate as well as Goddard’s Internal Research and Development (IRAD) program.